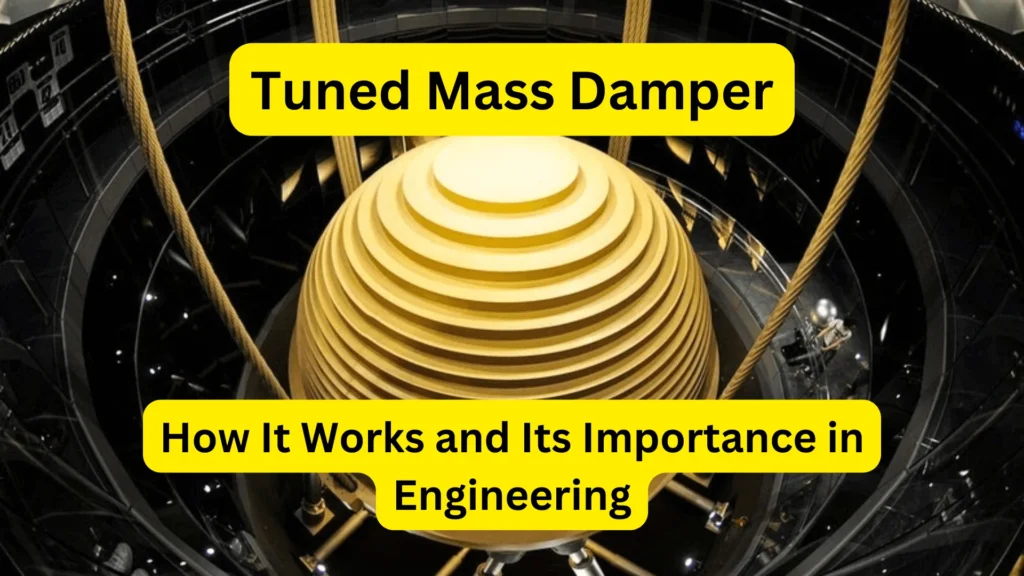
Introduction
Definition of a Tuned Mass Damper
A Tuned Mass Damper is a device specifically designed to reduce unwanted vibrations in structures, mechanical systems, or equipment. It consists of a secondary mass attached to a structure via a spring and damper mechanism, which works to counteract oscillations caused by external forces, such as wind, earthquakes, or human activities. It is finely tuned to the natural frequency of the structure, meaning it moves out of phase with the vibrations, effectively dissipating energy and reducing the amplitude of oscillations. By transferring the energy of the oscillations to the damper, the overall structural movement is minimized.
Tuned mass dampers come in various forms, such as passive, active, and semi-active systems, depending on the complexity of the damping system and the specific requirements of the structure. These devices are essential components in modern engineering, especially for tall buildings, bridges, and other large structures that are prone to vibrations due to environmental factors or dynamic forces.
Significance of TMD in Structural Engineering
Tuned Mass Dampers are crucial in structural engineering for mitigating vibrations and enhancing the stability of buildings and structures. Their significance lies in their ability to counteract resonance and dynamic forces that can cause excessive swaying or oscillations, especially in skyscrapers, bridges, and other tall structures. By effectively absorbing and dissipating vibrational energy, it reduces structural fatigue and extend the lifespan of these assets.
They also improve occupant comfort by minimizing perceptible movements in high-rise buildings and enhance safety during events like earthquakes and strong winds. Additionally, it contributes to the structural integrity of critical infrastructure by ensuring that dynamic loads do not compromise performance or safety. Their role in modern construction is vital, providing both practical and safety benefits while addressing complex engineering challenges.
Importance of Vibration Control in Modern Construction
In the field of modern construction, vibration control plays an integral role in both safety and comfort. Structures such as skyscrapers, bridges, and stadiums are subject to dynamic forces—whether from environmental phenomena like earthquakes and wind or from daily activities such as pedestrian or vehicular movement. These vibrations can cause discomfort for occupants, reduce the lifespan of the building materials, and, in severe cases, lead to structural damage or catastrophic failure.
Tuned Mass Dampers are one of the most effective methods for mitigating these vibrations. By adding a counterbalancing force that absorbs and neutralizes oscillations, it provides a more stable and resilient structure. In the case of tall buildings like Taipei 101 or Shanghai Tower, they are essential for reducing the swaying caused by high winds, ensuring the safety and comfort of the occupants. Similarly, on long-span bridges, such as the Millennium Bridge in London, they have been used to control vibrations induced by foot traffic, preventing resonance that could otherwise lead to structural fatigue.
As construction projects become increasingly ambitious and as the world faces more intense environmental conditions, the role of TMDs in ensuring longevity, resilience, and safety in structures becomes paramount. The application of TMDs has allowed engineers to innovate and push boundaries, knowing that they have a reliable solution to one of the most challenging aspects of structural design—vibration control. By incorporating them, we can build taller, longer, and more complex structures while maintaining the highest standards of structural safety and efficiency.
The Concept Behind Tuned Mass Dampers
What is a Mass Damper and How It Reduces Vibrations
A mass damper is a mechanical device used to reduce undesirable vibrations in a structure or system. Vibrations, especially harmonic or resonant vibrations, can cause significant damage or discomfort if left unchecked. The basic principle behind a tuned mass damper is to counteract these vibrations by using a secondary mass that moves in opposition to the motion of the main structure. The mass damper absorbs and dissipates vibrational energy, reducing the amplitude of oscillations and stabilizing the structure.
In simple terms, when a structure like a building or a bridge vibrates due to external forces (such as wind or earthquakes), it helps balance these forces by moving in the opposite direction of the vibrations. This action reduces the intensity of the vibrations, making the structure more stable. The system is “tuned” to the natural frequency of the structure, meaning it is designed to respond at the same frequency but in a way that neutralizes the resonance.
For example, in a crankshaft torsional damper, the damper reduces harmful vibrations in a rotating engine component by converting kinetic energy into heat via friction or hydraulic mechanisms. Similarly, TMDs in buildings and bridges ensure that worst-case vibrational scenarios are less intense, contributing to both the longevity and safety of the structure.
Key Components of a TMD
A Tuned Mass Damper consists of three key components:
- Mass: The secondary mass is the part that moves to counterbalance the vibrations in the primary structure. This mass can range from small weights in machines to large, heavy pendulums in skyscrapers. The size of the mass is critical, as it needs to be large enough to have a significant effect on the vibrations. In some systems, this secondary mass is about 10% of the primary structure’s mass.
- Spring: The spring provides the restoring force for the system. It is designed to return the mass to its original position once the external force has been neutralized. The stiffness of the spring determines the system’s natural frequency and plays a crucial role in tuning the damper. By adjusting the spring’s stiffness, it can be optimized to counteract specific frequencies of vibration.
- Damping System: The damping mechanism dissipates the energy absorbed by the mass as it moves. Typically, the damping system uses frictional or hydraulic components to convert mechanical energy into heat, similar to how an automotive shock absorber works. The damping coefficient determines how quickly the energy is dissipated, which in turn affects the reduction of vibrational amplitude.
Together, these components form a simple spring-mass-damper system that is fine-tuned to reduce the effects of resonance. The damper doesn’t completely eliminate vibrations but instead mitigates them to a level that is safe and manageable.
Physics Behind Tuning the System to Counteract Resonance
The effectiveness of a Tuned Mass Damper lies in its ability to counteract resonance, a condition where the natural frequency of a structure matches the frequency of external forces, causing large oscillations. The goal of a it is to tune its own frequency to match the natural frequency of the structure, but in a way that reduces the harmful effects of resonance.
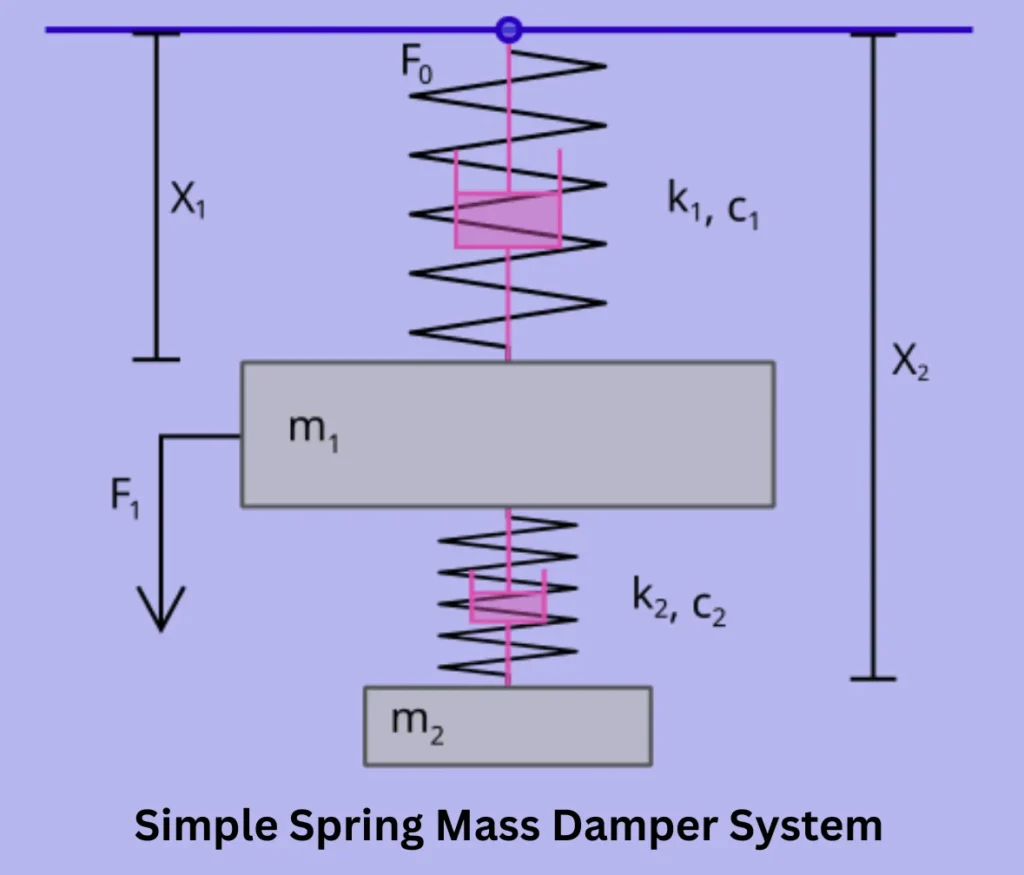
In a simple spring-mass-damper system, imagine a motor with a primary mass, m1, mounted on soft motor mounts. As the motor vibrates, the mounts experience a force F0 and act as both a spring k1 and a damper, c1. To reduce the force on the motor mounts, a smaller secondary mass m2 is connected to the primary mass via its own spring k2 and damper c2. The secondary mass m2 moves in response to vibrations, effectively reducing the force F1 acting on the motor by out-of-phase motion.
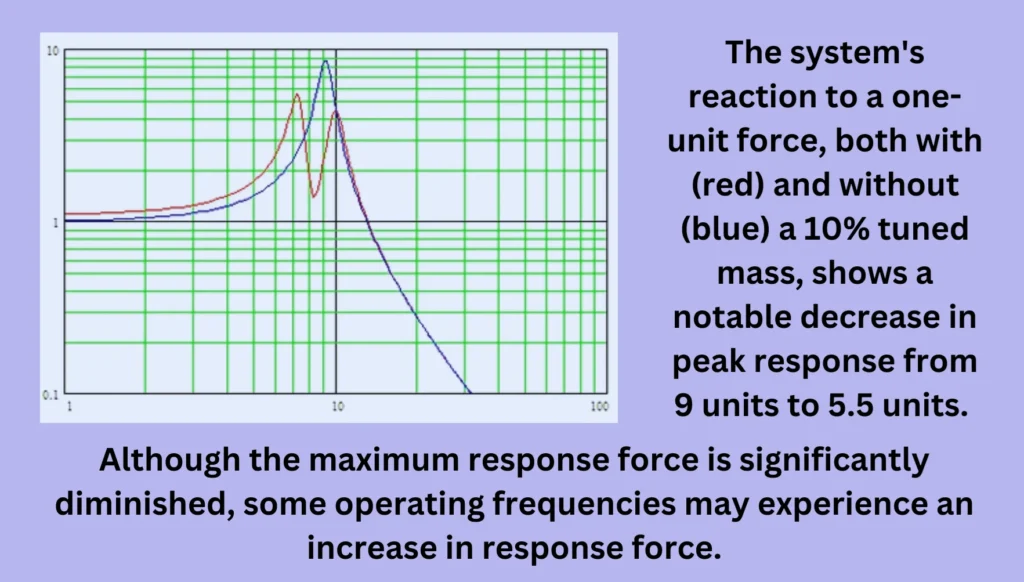
Its effectiveness is illustrated in a graph of the system’s response to vibrations. In the baseline case, without a TMD, the system exhibits a maximum response of 9 units of force at a frequency of around 9 units. After adding a tuned mass damper (10% of the primary mass), the response drops to 5.5 units at a slightly lower frequency of 7. However, the system also develops a second mode of vibration at lower frequencies, highlighting the balance between reducing peak resonances and potentially introducing new, smaller peaks.
The height of the peaks can be adjusted by changing the spring stiffness and damping. When the damping mass m2 moves out of phase with the primary mass m1 it pulls on the primary mass in the same direction as the external force, maximizing the damping effect and minimizing the overall vibrations. At frequencies where m2 moves 180° out of phase with m1, the damper system is most effective, as it maximizes the energy dissipated by c2, the damping component.
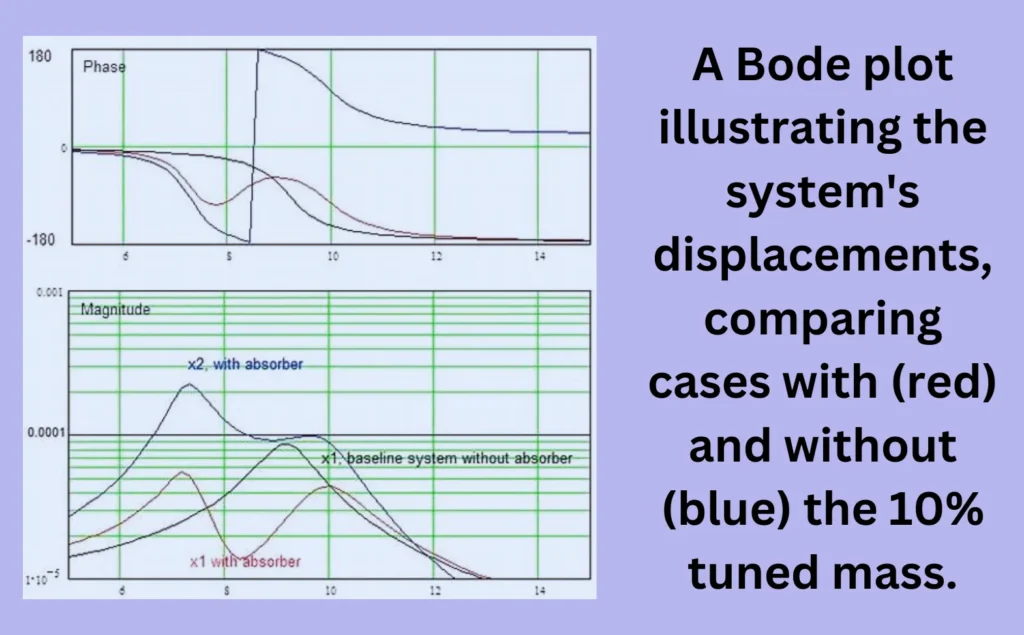
A Bode plot, which shows both the magnitude and phase of the motion for each mass, further illustrates how it alters the dynamic behavior of the system. As the frequency increases, the damping mass moves out of phase with the primary mass, optimizing the vibration reduction. This phase shift, particularly at around 9.5 Hz, is where it excels, minimizing vibration by maximizing the relative motion between the two masses.
In essence, it works by creating a controlled counter-motion that opposes the vibrations in the main structure. The tuning of the system ensures that the damper can effectively neutralize the vibrations at the critical resonance frequency, reducing the overall motion and protecting the structure from excessive stress. By carefully adjusting the mass, spring stiffness, and damping coefficient, engineers can fine-tune it to match the specific dynamic characteristics of a structure, ensuring that it provides optimal vibration control.
This sophisticated balance between mass, spring, and damper is what allows it to play such a vital role in modern engineering, stabilizing structures and preventing damage caused by harmful resonant vibrations.
Applications of Tuned Mass Dampers in Engineering
Tuned Mass Dampers are widely used in various engineering fields to reduce vibrations and enhance the stability of structures or systems. Their ability to mitigate resonance and vibrations makes them crucial in high-performance and sensitive environments. Below are some of the most prominent applications of TMDs in different fields of engineering:
Skyscrapers and Tall Buildings
In skyscrapers, particularly tall and slender buildings, wind-induced vibrations can cause significant swaying, which may be uncomfortable or even dangerous for occupants. To mitigate this, TMDs are installed to counteract the forces caused by wind or seismic activity. One of the most famous examples of it is in a skyscraper is the Taipei 101 building in Taiwan.
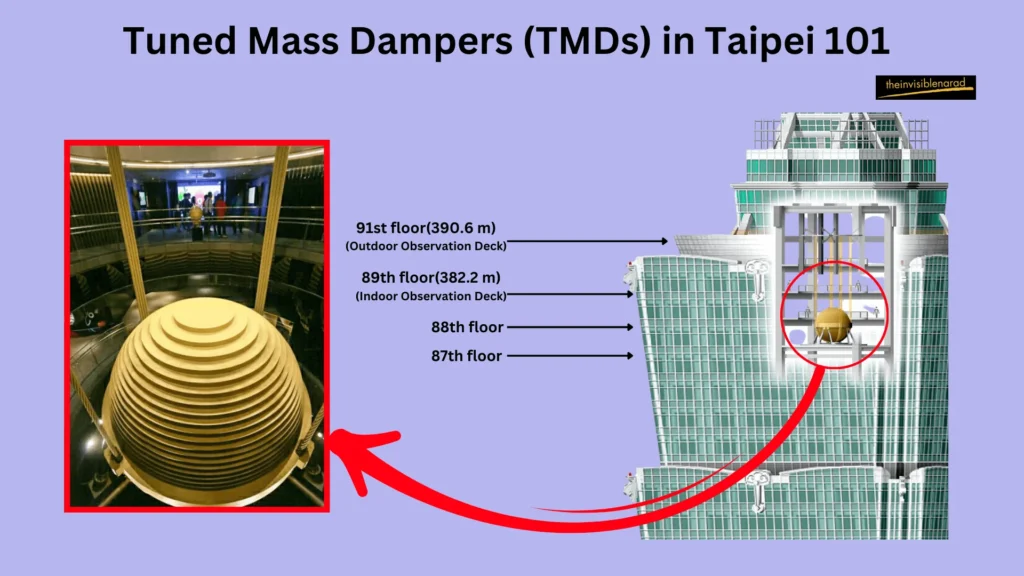
Taipei 101
This building features a massive TMD that weighs 660 metric tons and is suspended between the 87th and 91st floors. It is a pendulum-style damper, designed to counterbalance the building’s swaying caused by typhoons or earthquakes. This system has been instrumental in stabilizing the skyscraper during strong winds and tremors, making it an essential safety and comfort feature for both the structure and its occupants.
Bridges: TMDs in Large Suspension Bridges
Bridges are another common structure where they are employed, especially in large suspension bridges prone to resonance from pedestrian or vehicular traffic.
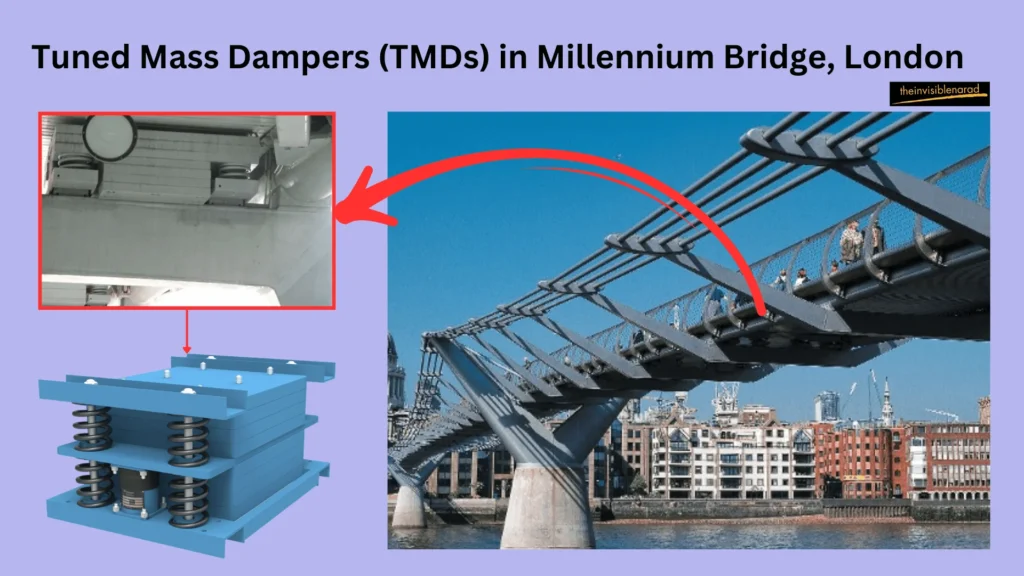
Millennium Bridge, London
The Millennium Bridge became famous for its swaying motion when it opened in 2000 due to pedestrian-induced vibrations. The bridge’s natural frequency matched that of people walking, causing resonance. To resolve this issue, engineers installed them to reduce the oscillations and prevent further swaying. They have since stabilized the structure, ensuring safe pedestrian movement. TMDs in bridges help to reduce not only the impact of traffic loads but also vibrations from environmental forces like wind, preventing fatigue and structural damage over time.
Spacecraft
In spacecraft, vibration control is crucial for maintaining the integrity of delicate components during launch and space travel. Thes are used to reduce vibrations caused by rocket engines and other mechanical systems.
NASA’s Ares Solid Fuel Booster
NASA proposed the use of 16 tuned mass dampers in their design to reduce peak vibration loads from 6g to 0.25g. They are responsible for reducing loads from 1g to 0.25g, were a part of the overall strategy to enhance vibration control in space missions. This significant reduction is essential to prevent structural failure or malfunction of sensitive equipment during launch. Their use in spacecraft ensures that the mechanical systems and scientific instruments remain functional, especially in high-vibration environments like rocket launches.
Power Transmission Lines
Power transmission lines often face vibrational forces from wind, which can cause damage to the wires or lead to metal fatigue. To counteract this, Stockbridge dampers are commonly used.
Stockbridge Dampers
These are barbell-shaped devices that hang from transmission lines. They help reduce high-frequency, low-amplitude oscillations, commonly referred to as flutter. By dissipating vibrational energy, these dampers prolong the lifespan of power lines and ensure the continuity of electrical transmission, even under harsh environmental conditions. Without them, power lines would experience more frequent wear and tear, increasing maintenance costs and the risk of failures.
Wind Turbines
Wind turbines are subject to significant vibrational stress due to wind gusts and varying loads during operation. To manage these vibrations, they are employed to enhance the operational stability and durability of the turbines.
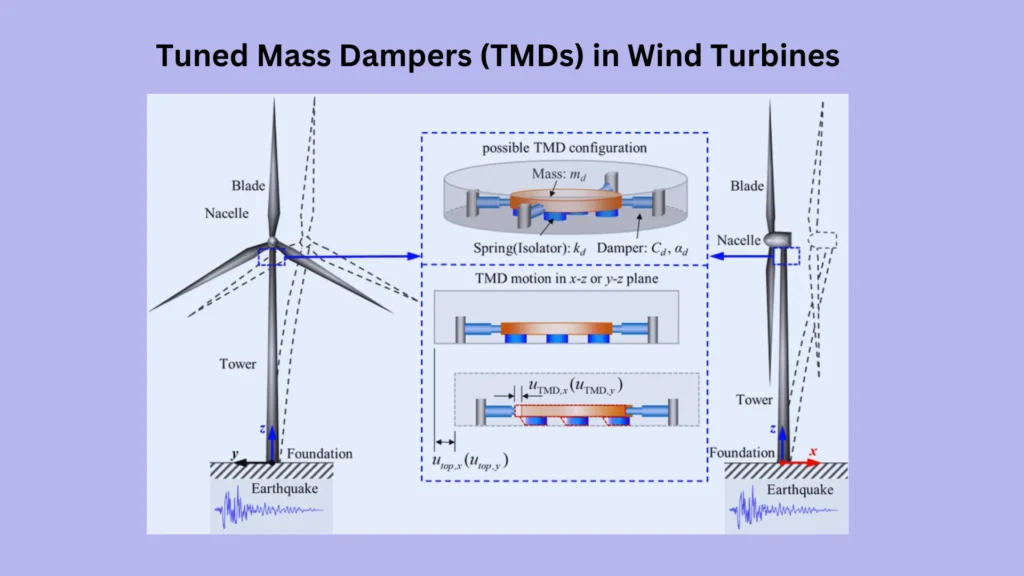
TMDs in Wind Turbines
In a typical wind turbine, it consists of an auxiliary mass attached to the main structure through springs and damping elements. It is tuned to oscillate out of phase with the motion of the turbine structure, absorbing energy and reducing the vibrations. In some designs, an auxiliary mass is hung below the nacelle of the turbine to act as a damper. These dampers play a vital role in maintaining the efficiency and safety of wind turbines, which are often located in windy environments that induce continuous stress on the structure.
Automobiles
They are widely used in automobiles to reduce vibrations in engines and other mechanical systems, improving performance, comfort, and durability.
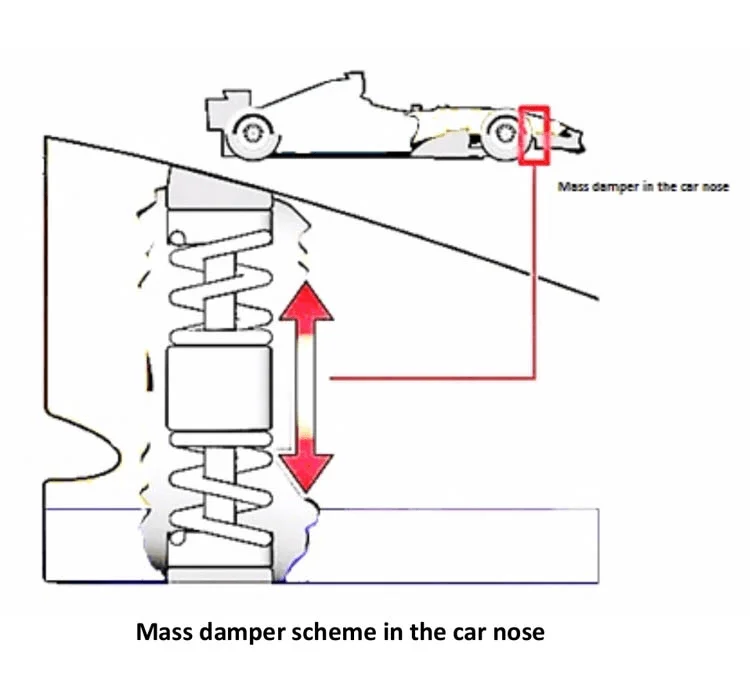
- Motorsport: In motorsports, they have been employed to optimize performance by reducing vibrations that affect the handling and stability of race cars. For example, Renault introduced a tuned mass damper system in their 2005 F1 car, the Renault R25, which contributed to a significant reduction in lap times by 0.3 seconds. However, the system was later deemed illegal by the FIA due to its influence on the car’s aerodynamics, as the damper was not rigidly attached to the chassis.
- Production Cars: In everyday automobiles, they are commonly found in the crankshaft pulley to manage torsional vibrations. These dampers, often called harmonic dampers, consist of a band of rubber that helps reduce vibrations in the engine, improving the smoothness and lifespan of the engine components. Additionally, they are used in driveline systems to mitigate noise and vibrations that could otherwise degrade performance or cause discomfort to passengers.
Some cars, like the Citroën 2CV, even integrated tuned mass dampers in the suspension system to enhance ride comfort by reducing the vehicle’s overall vibration. This highlights the versatile application of TMDs in the automotive sector.
Types of Tuned Mass Dampers
Tuned Mass Dampers come in various forms, each designed to manage vibrations under specific conditions and for different structural or mechanical needs. These dampers are categorized based on their operational mechanics and the types of structures they are used in. In this section, we will explore the different types of TMDs, their features, and their respective applications in engineering and construction.
Passive Tuned Mass Dampers: Common and Widely Used
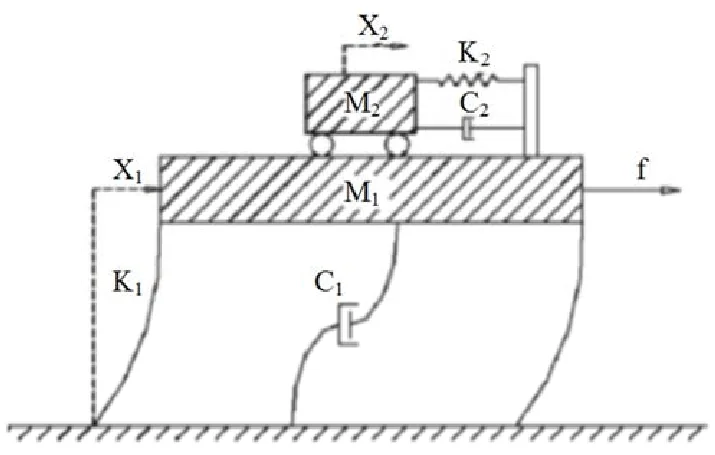
Passive Tuned Mass Dampers are the most common and widely used type of TMD. These systems are self-regulating and do not require external power or active control mechanisms to function. They consist of a mass, spring, and damper that work together to reduce vibrations by oscillating out of phase with the structure they are protecting. Key Features of Passive TMDs:
- No External Power: Passive TMDs rely on mechanical properties and do not require power to operate. Once installed, they function autonomously by absorbing vibrational energy.
- Simplicity and Reliability: Due to their simple design, they are highly reliable and have fewer maintenance requirements. They are also easier and less expensive to install compared to more advanced types.
- Wide Applications: Passive TMDs are used in a variety of structures such as buildings, bridges, and machinery. Their effectiveness in reducing vibrations from environmental forces, such as wind or seismic activity, makes them suitable for many different engineering scenarios.
- Example
- Taipei 101: The pendulum-style TMD in Taipei 101 is a passive damper that helps the building withstand strong winds and earthquakes by reducing its sway. The system works without any active control, relying purely on the mechanics of its mass and springs.
- Limitations
- While they are effective for many standard applications, their lack of adaptability means they may not perform optimally in conditions where vibrational frequencies change dynamically. In such cases, more advanced types of TMDs, like active or semi-active systems, are required.
Active Tuned Mass Dampers (ATMDs) and Semi-Active Tuned Mass Dampers (SATMDs) are more sophisticated systems that use external controls to enhance vibration mitigation. These dampers are designed for environments where vibrations vary over time or where precise control is necessary. Key Features of Active TMDs:
Active and Semi-Active Tuned Mass Dampers: Advanced, Controlled Systems
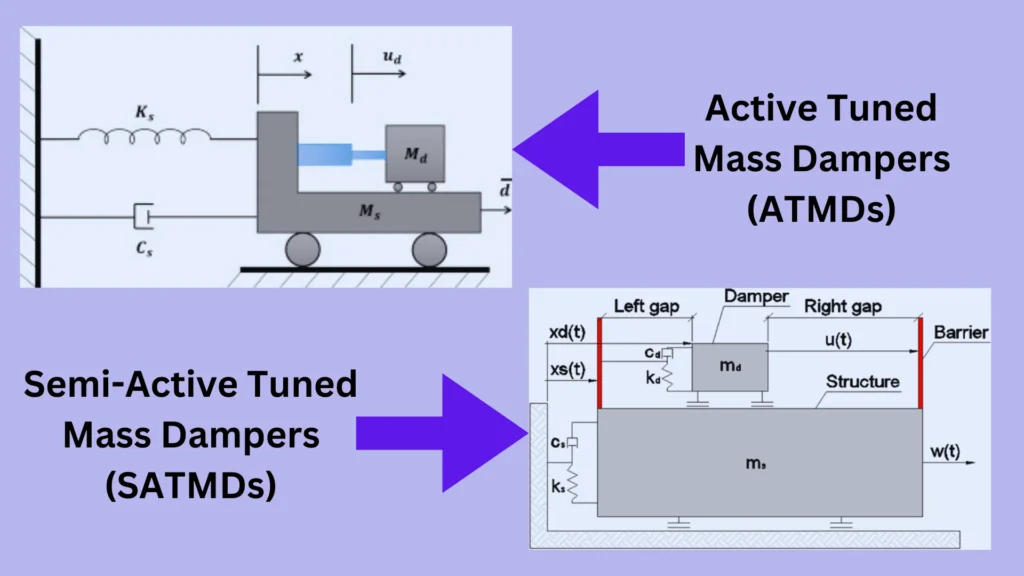
- External Control Mechanism: Active TMDs use sensors, actuators, and a power source to monitor vibrations in real time and adjust the damper’s response accordingly. This allows for a dynamic response to varying vibration frequencies.
- Enhanced Performance: By actively controlling the damper, ATMDs can achieve higher levels of vibration reduction compared to passive systems. They are ideal for structures that experience changing environmental conditions, such as varying wind speeds or seismic activity.
- Power Requirement: Active TMDs require continuous power to operate. They use feedback systems to detect vibrations and activate the appropriate counterforces to neutralize them.
Semi-Active TMDs offer a middle ground between passive and active systems. They do not require as much power as ATMDs but still allow some degree of adjustability through variable damping mechanisms. For instance, SATMDs can modify their damping properties in response to changing vibration frequencies, making them more adaptive than passive systems but less complex and power-intensive than fully active ones.
Applications of Active and Semi-Active TMDs:
- High-Tech Infrastructure: ATMDs are often used in cutting-edge structures, such as high-tech laboratories or sensitive industrial machinery, where vibration control must be extremely precise to avoid interference with delicate processes.
- Skyscrapers: In some skyscrapers, active dampers are installed to dynamically adjust to varying wind conditions, enhancing structural safety and comfort for occupants.
- Example
- John Hancock Tower (Boston): This skyscraper has been retrofitted with an active mass damper to manage sway caused by wind. The system uses real-time data to adjust its damping force, maintaining stability and comfort within the tower.
- Limitations
- The primary limitation of ATMDs is their dependence on external power and complex control systems. They are also more expensive to install and maintain compared to passive systems. Moreover, any disruption in the power supply can render the system ineffective.
Liquid and Pendulum Dampers: Specialized Forms of TMDs
In addition to the passive and active categories, there are specialized forms of TMDs, such as liquid dampers and pendulum dampers, that offer unique solutions for vibration control.
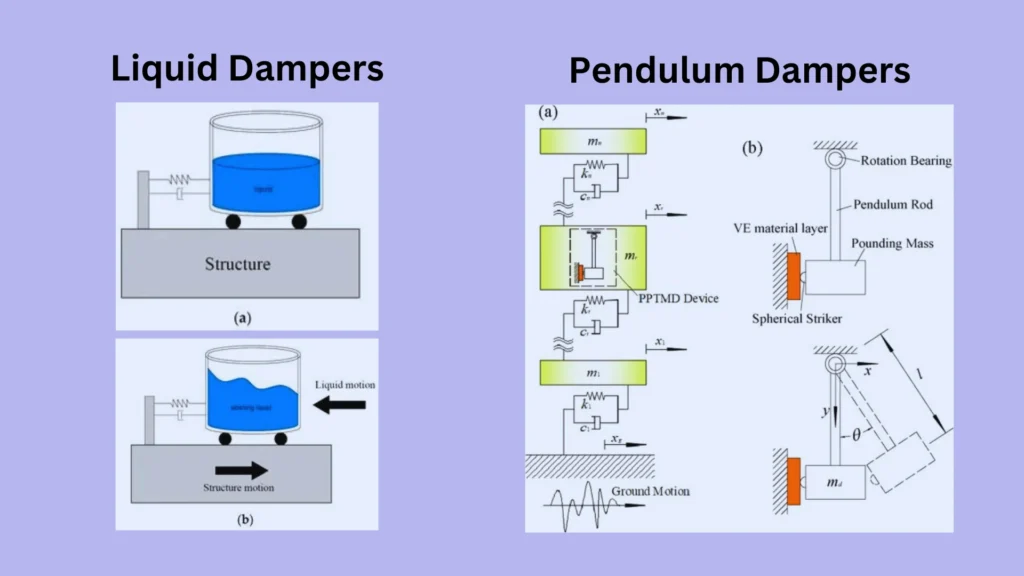
Liquid Tuned Mass Dampers
Liquid dampers use fluid masses to absorb and dissipate vibrational energy. In these systems, the fluid (often water or oil) is contained in a sealed chamber and moves in opposition to the vibrations of the structure. The fluid’s motion, combined with damping devices such as baffles or orifices, helps reduce the amplitude of vibrations. Key Features of Liquid Dampers
- High Damping Capability: Liquid dampers are particularly effective at absorbing large amounts of vibrational energy, making them suitable for structures experiencing heavy or complex vibrational forces.
- Flexibility: The behavior of liquid dampers can be modified by adjusting the fluid’s properties, the shape of the chamber, or the size of the damping orifices, making them adaptable to various applications.
- Applications
- Offshore Oil Platforms: Liquid dampers are often used in structures like offshore oil platforms to reduce vibrations caused by wave action. These dampers help stabilize the platforms, enhancing both safety and operational efficiency.
Pendulum Tuned Mass Dampers
Pendulum TMDs are a common type of passive TMD used primarily in tall structures, where large oscillations need to be countered. These systems use a pendulum-like mass that swings in the opposite direction of the building’s motion, creating a counteracting force that reduces vibrations. Key Features of Pendulum Dampers:
- Effective for Tall Buildings: Pendulum dampers are particularly useful in skyscrapers and towers, where wind or seismic activity can cause significant swaying.
- Low Maintenance: Since pendulum systems are mechanically simple, they require minimal maintenance compared to more complex damping systems.
- Applications
- Tokyo Skytree: The Tokyo Skytree features a pendulum-style TMD, which helps counteract the tower’s swaying caused by earthquakes and strong winds. The pendulum’s natural movement creates a damping force that stabilizes the structure without the need for external power or control systems.
Benefits of Using Tuned Mass Dampers
Tuned Mass Dampers provide crucial benefits in modern engineering, particularly in enhancing the structural integrity, safety, and comfort of buildings and various mechanical systems. Their ability to manage vibrations from environmental forces such as wind, seismic activity, and even mechanical disturbances makes them indispensable in large structures like skyscrapers, bridges, and other engineering marvels. This section outlines the key benefits of using them in construction and engineering, focusing on reducing structural fatigue, improving occupant comfort, and enhancing safety during dynamic forces.
Reducing Structural Fatigue and Increasing the Lifespan of Buildings
One of the most significant benefits of using Tuned Mass Dampers is their ability to reduce structural fatigue. Structures like skyscrapers, bridges, and transmission towers are exposed to continual environmental forces such as wind, seismic activity, and even human-induced vibrations. Over time, these forces can lead to structural fatigue, which accelerates wear and tear, ultimately compromising the lifespan of the building or structure.
How they Reduce Structural Fatigue
- Damping Vibrational Energy: By absorbing and redistributing vibrational energy, they reduce the stress placed on structural components. Instead of allowing the vibrations to travel unchecked through the building’s materials, it works to neutralize these forces, thereby reducing the strain on beams, joints, and foundations.
- Minimizing Oscillations: Skyscrapers and tall structures often experience oscillations due to wind and seismic forces. These oscillations, if left unmanaged, can lead to material degradation over time. They help to minimize these oscillations, preventing repetitive strain and maintaining the structure’s integrity for a longer period.
- Decreasing Maintenance Needs: As a result of reduced structural fatigue, the overall maintenance costs of a building or structure are lowered. Components such as beams, joints, and welds experience less wear and require fewer repairs or replacements over the building’s lifecycle.
- Example: The Citigroup Center in New York City is a prime example of how they can increase a building’s longevity. The skyscraper’s TMD helps mitigate the effects of wind-induced vibrations, reducing the stress on the structure’s foundation and supporting framework. This has significantly extended the lifespan of the building, minimizing the need for expensive repairs and reinforcement.
Improved Comfort for Occupants in High-Rise Buildings
Tuned Mass Dampers play a vital role in improving the comfort of occupants in high-rise buildings. Tall buildings are particularly susceptible to sway caused by wind and seismic forces, and this can result in discomfort for people living or working in upper floors. Uncontrolled swaying can cause motion sickness, vertigo, and a general sense of unease among occupants. They help to mitigate these effects by stabilizing the building’s movements.
How TMDs Improve Occupant Comfort
- Sway Reduction: High-rise buildings naturally sway in response to wind loads, especially at higher altitudes. This movement can be noticeable and uncomfortable for occupants, even leading to motion sickness in extreme cases. They reduce this sway by counteracting the building’s motion, creating a more stable and comfortable environment.
- Lowered Motion Perception: They not only reduce the amplitude of a building’s vibrations but also lower the frequency at which they occur. This means that occupants perceive less motion, especially in scenarios where frequent vibrations (such as strong winds) are the norm.
- Consistent Comfort Across Different Floors: In tall skyscrapers, the movement tends to be more pronounced on the upper floors. They ensure that comfort is maintained throughout the entire building by mitigating sway from top to bottom.
- Example: The Taipei 101 skyscraper employs a large pendulum TMD system to stabilize the building during typhoons and earthquakes. Without them occupants on the upper floors would experience significant discomfort due to the building’s natural sway. The pendulum damper ensures that vibrations are kept to a minimum, providing a stable and comfortable experience for all occupants, especially those in the upper levels.
Enhanced Safety During Earthquakes, Strong Winds, and Other Dynamic Forces
Perhaps the most critical advantage of Tuned Mass Dampers is their ability to enhance safety in buildings and structures during extreme events like earthquakes, strong winds, and other dynamic forces. These natural phenomena can cause buildings to sway, buckle, or even collapse if not adequately managed. TMDs offer an effective solution by actively counteracting the forces at play, preventing catastrophic structural failures.
How TMDs Enhance Safety
- Seismic Protection: During an earthquake, seismic waves cause buildings to oscillate at various frequencies, which can be dangerous if the natural frequency of the building aligns with the earthquake’s vibrations. They are often tuned to the natural frequency of the building, reducing its oscillations and preventing excessive sway that could lead to structural failure.
- Wind Load Management: In regions prone to high winds, such as coastal or mountainous areas, tall buildings can experience significant stress from wind loads. They help counteract this by damping the oscillations caused by wind forces, reducing the risk of structural damage or collapse.
- Prevention of Resonance: Resonance, where the frequency of external forces matches the natural frequency of a structure, can lead to excessive vibrations that could cause parts of a building or bridge to fail. They prevent resonance by changing the vibrational characteristics of the structure, ensuring that external forces do not align with the structure’s natural oscillations.
- Example: The Millennium Bridge in London experienced significant sway when pedestrians crossed it in large numbers, a phenomenon known as synchronous lateral excitation. To address this, they were installed to dampen the bridge’s lateral vibrations, effectively ensuring the safety of pedestrians and preventing potential structural damage.
Earthquake and Wind Safety in Skyscrapers
Skyscrapers, especially those located in earthquake-prone or typhoon-affected regions, benefit immensely from the integration of TMDs. During an earthquake or severe storm, it acts as a counterweight, reducing the movement of the structure and ensuring that the building can withstand the forces without sustaining critical damage.
The Shanghai Tower, the world’s second tallest building, has incorporated a TMD to safeguard the structure against high winds and seismic activity. Without the TMD, the immense height of the building could make it vulnerable to wind and earthquake forces, endangering both the structure and its occupants.
Challenges and Limitations
While Tuned Mass Dampers are a highly effective solution for reducing structural vibrations, their application in modern engineering and construction comes with certain challenges and limitations. These include cost considerations, ongoing maintenance needs, and the difficulties associated with customizing them for specific structures.
Cost Considerations in Installing TMD Systems
One of the most significant challenges in the adoption of Tuned Mass Dampers is the high cost associated with their installation. TMD systems are complex, requiring precise engineering, specialized materials, and often large-scale construction work, particularly for high-rise buildings and large bridges.
Key Factors Contributing to the Cost
- Initial Design and Engineering: Designing a TMD system that is specifically tailored to a building’s unique characteristics involves detailed modeling and analysis, which can be expensive. Each structure has its own resonance frequencies and external force factors (e.g., wind, seismic activity), and designing a TMD that can mitigate these forces requires a high level of customization.
- Materials: High-quality materials are essential to ensure that TMD systems are durable and effective. This often means using heavy concrete, steel, and sophisticated hydraulic or spring systems, all of which drive up costs.
- Construction and Installation: Installing a TMD, especially in tall buildings or bridges, can require significant modifications to the structure. The construction work involved can be time-consuming and labor-intensive, further increasing the overall cost.
- Example: The Taipei 101 TMD, which weighs 660 metric tons and is suspended between the 88th and 92nd floors, required substantial investment in both materials and engineering design. All this resulted in an investment of US$4 million. The sheer size of the damper and the precision required for its installation contributed significantly to the overall cost of the skyscraper’s construction.
Maintenance Requirements for Optimal Performance
TMD systems require regular maintenance to ensure they continue to function properly over the lifespan of the structure. Without consistent upkeep, TMDs can degrade, which may lead to reduced efficiency in mitigating vibrations and increased wear on the building or structure itself.
Maintenance Challenges
- Wear and Tear: Over time, components of the TMD such as springs, dampers, and hydraulic systems can wear down due to constant use and exposure to environmental factors. Regular inspections and replacements are necessary to maintain optimal performance.
- Monitoring Systems: Some TMD systems, particularly active TMDs, rely on sophisticated sensors and control systems to adjust their behavior in real time. These systems need to be regularly monitored and updated to ensure they are functioning correctly.
- Access for Repairs: Accessing the TMD, particularly in tall skyscrapers or large suspension bridges, can be challenging. Repairs or adjustments may require temporary structural modifications, which can further add to maintenance costs.
- Example: The Millennium Bridge in London, which uses TMDs to counter pedestrian-induced vibrations, requires regular monitoring to ensure that the system continues to provide adequate damping. Over time, the dampers must be inspected and, if necessary, replaced to ensure the bridge remains safe for public use.
Design Challenges: Customizing TMD for Specific Structures
Designing a Tuned Mass Damper that is perfectly tuned to a specific building, bridge, or other structure can be complex. Each structure is unique in terms of its height, mass, natural frequency, and the environmental forces it is exposed to, which means that a one-size-fits-all approach does not work with TMD systems.
Design Customization Issues
- Natural Frequency Matching: One of the main design challenges is accurately tuning the TMD to the natural frequency of the structure. If the tuning is even slightly off, the system may not perform as effectively in dampening vibrations.
- Space and Weight Constraints: Installing a large, heavy TMD in a building or structure often requires significant design modifications. For skyscrapers, this might involve creating additional space for the damper, which can be difficult in terms of architectural planning.
- Complex Modeling: Engineers must use advanced computational models to predict how the TMD will perform in real-world conditions, which can be influenced by variables like wind speeds, temperature changes, and even pedestrian movements. Designing a TMD that can handle all these variables is a significant challenge.
Future Trends in Tuned Mass Dampers
As technology evolves, new trends are emerging that promise to revolutionize how Tuned Mass Dampers are designed and implemented. These advances include the integration of artificial intelligence (AI) in active systems, a shift toward more sustainable designs, and expanding the use of TMDs in futuristic construction and industries.
Advances in Active TMD Systems
One of the most exciting future trends in TMD technology is the integration of artificial intelligence (AI) and real-time data systems into active and semi-active TMDs. Unlike passive systems, which have a fixed response, active TMDs can adapt their behavior in response to changing conditions, such as variations in wind speed or seismic activity.
Key Innovations
- Real-Time Monitoring: Active TMDs can use real-time data from sensors placed throughout the structure to adjust their damping response on the fly, ensuring the most efficient mitigation of vibrations.
- AI Algorithms: AI-driven algorithms can analyze environmental and structural data to predict and adjust for potential vibrations, making active TMD systems more efficient and responsive.
- Self-Tuning Systems: AI could enable TMDs to self-tune, automatically adjusting their settings to optimize performance as the building’s natural frequencies change over time due to environmental factors or aging materials.
Sustainable Designs
As the world moves toward more sustainable construction practices, there is growing interest in developing TMDs that are environmentally friendly and energy efficient. This includes using recycled materials in TMD construction and designing systems that minimize energy consumption.
Sustainability Innovations
- Eco-Friendly Materials: Future TMD designs may use more sustainable materials, such as recycled metals or biodegradable polymers, reducing the environmental impact of their production and installation.
- Energy Harvesting: Some advanced TMD systems are being designed to harvest energy from the vibrations they mitigate. This energy could then be used to power the building’s systems or be stored for later use, creating a more sustainable energy solution.
Potential in Futuristic Construction and Industries
As cities grow taller and structures become more complex, the use of TMDs will expand into new industries and types of construction. From space stations to underground infrastructure, TMDs could become an essential tool in managing vibrations in a wide range of futuristic applications.
New Applications
- Space Exploration: In space stations or other orbital structures, TMDs could be used to mitigate vibrations caused by docking spacecraft, micro-meteoroid impacts, or other external forces.
- Underground Cities: With growing interest in underground construction, TMDs may become essential for reducing vibrations caused by seismic activity or nearby transportation systems.
- Advanced Robotics and Industrial Machinery: TMDs could also find new applications in robotics, where precision is critical, or in heavy industrial machinery, where controlling vibrations is essential for efficient operation.
Conclusion & FAQs
Tuned Mass Dampers have become an integral part of modern engineering, providing vital benefits in reducing vibrations, enhancing structural stability, and improving occupant comfort. They are used extensively in high-rise buildings, bridges, wind turbines, and other structures, helping to protect against environmental forces such as wind, seismic activity, and pedestrian-induced oscillations. By extending the lifespan of buildings and ensuring safety, they have revolutionized modern construction.
Looking ahead, they will continue to play a critical role in the evolution of sustainable construction, integrating AI and real-time data systems to improve performance and energy efficiency. As structures become more complex and environmental challenges intensify, the role of TMDs in ensuring the safety and comfort of buildings and infrastructure will only become more important.
As cities grow and engineering challenges increase, architects and engineers must prioritize vibration control in their designs. By incorporating TMD systems into the early stages of planning, they can ensure that buildings are not only structurally sound but also safe and comfortable for occupants. The future of construction will depend on smart, adaptable solutions like Tuned Mass Dampers to protect our buildings and infrastructure against the forces of nature.
Frequently Asked Questions (FAQs)
What is a TMD, or tuned mass damper?
A Tuned Mass Damper is a device used in engineering to reduce the amplitude of mechanical vibrations. It consists of a mass attached to a structure by means of springs or other elastic elements. The TMD works by moving in opposition to the vibration of the structure, effectively dampening oscillations caused by external forces such as wind, seismic activity, or human movement.
How do Tuned Mass Dampers work?
Tuned Mass Dampers work by counteracting the forces that cause vibrations in structures. When a building or structure vibrates, the TMD’s mass moves in the opposite direction of the vibration, reducing the amplitude of the oscillations. This is achieved by tuning the TMD to match the structure’s natural frequency, allowing it to effectively absorb and dissipate the energy of the vibration.
How do TMDs improve safety during earthquakes?
They reduce the swaying and oscillations caused by seismic waves during earthquakes. By absorbing the energy from these movements, TMDs help prevent structural damage and ensure the safety of occupants. They are a key component in earthquake-resistant design, especially for tall buildings in seismically active regions.
Are Tuned Mass Dampers environmentally friendly?
TMDs themselves are not inherently eco-friendly, but newer designs are incorporating sustainable materials and energy-efficient technologies. Some advanced TMD systems can even harvest energy from vibrations, contributing to a more sustainable building design.
Can Tuned Mass Dampers be retrofitted into existing structures?
Yes, Tuned Mass Dampers can be retrofitted into existing structures, but the process can be complex and expensive. The installation requires careful analysis of the building’s resonance frequencies and vibration issues, and modifications to the structure may be necessary to accommodate the damper.
How long do Tuned Mass Dampers last?
The lifespan of a TMD depends on the materials used and the maintenance schedule. With regular upkeep, such as inspections and replacements of worn components, TMDs can last for decades, particularly in well-maintained structures like skyscrapers and bridges.
What future trends are expected in TMD technology?
Future trends in TMD technology include:
1. AI integration: Active TMDs that use artificial intelligence to adjust in real-time based on environmental conditions.
2. Sustainability: The use of eco-friendly materials and energy-harvesting TMD systems.
3. New applications: Expansion into new industries such as space exploration, robotics, and underground infrastructure.How do TMDs in automobiles differ from those in buildings?
In automobiles, TMDs are used to reduce vibrations in various parts of the vehicle, such as the crankshaft, driveline, or suspension system. These are typically smaller and less complex than the massive TMDs used in skyscrapers, but they serve a similar purpose in enhancing comfort and performance by reducing mechanical vibrations.